Have you ever wondered why there are a multitude of sensor output signals that can be configured on pressure, temperature, humidity, or gas measuring devices used in Process or HVAC applications?
Understanding Sensor Output Signals
Have you ever wondered why there are a multitude of sensor output signals that can be configured on pressure, temperature, humidity, or gas measuring devices used in Process or HVAC applications? Most of these outputs were originally established to allow sensor manufacturers to better interface with the inputs provided by programmable logic controller (PLC) and direct digital controller (DDC) manufacturers, which are used to control processes for both process automation and HVAC control.
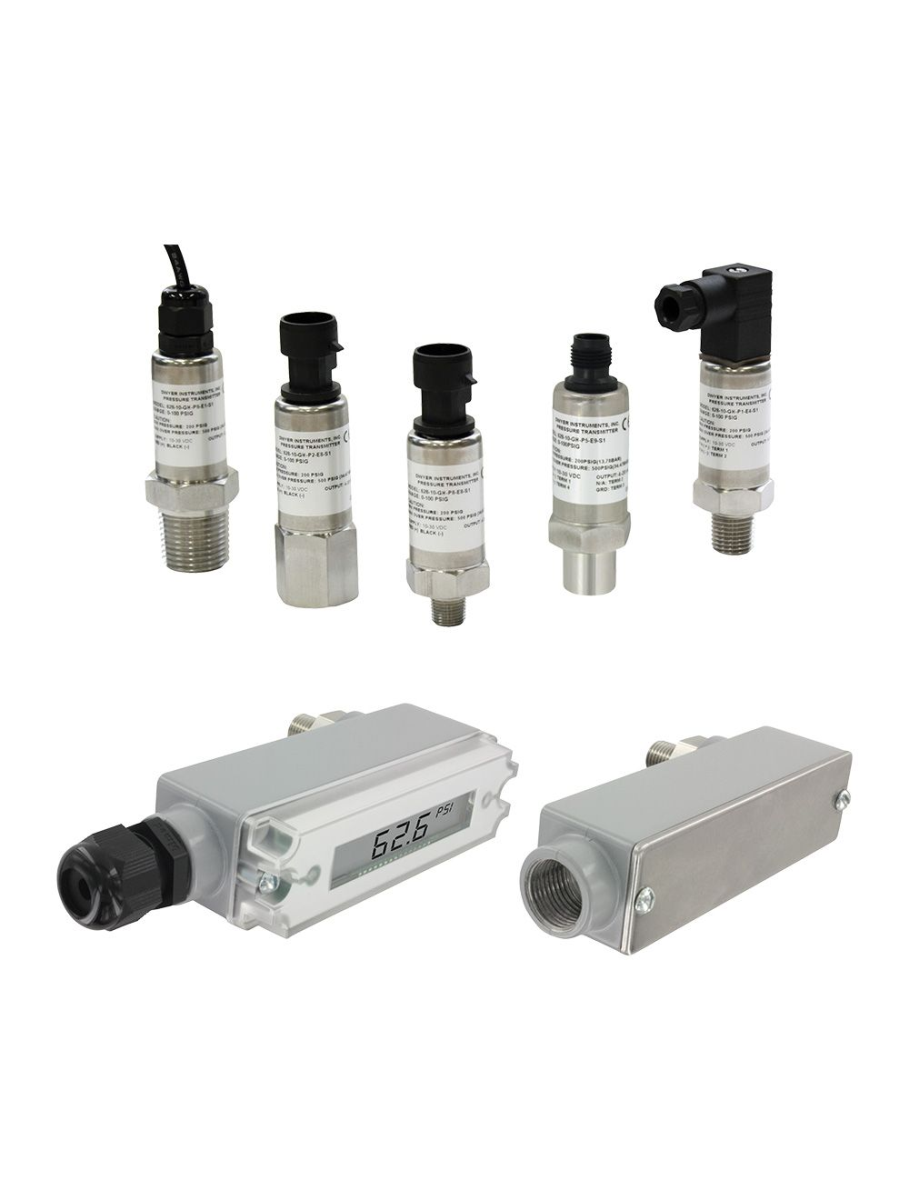
Let's focus on two of the most commonly used output signals and concentrate on the advantages and/or disadvantages that these output signals bring. Two of the most commonly used output signals include the analog current output, typically 4-20mA, and the voltage output, typically 0-10V.
The 0-10V analog voltage output is one of the most common output signals used on Process Instruments and HVAC equipment; due to the number of industrial controllers that will accept this signal input. Installers and technicians frequently comment on the ease of verification of the signal. One can simply connect a voltmeter in series to read the voltage and correlate that reading to the range on the sensor. When working with a 4-20mA analog current, reading the corresponding output signal can be more complex. Usually, a precision resistor needs to be used in conjunction with the sensor to convert the analog signal into a voltage signal (Ohm's Law) that allows measurement on a voltmeter. Sensors incorporating a 0-10V signal are also more susceptible to electrical noise from devices such as motors or relays leading to inaccurate output signals where a 4-20mA analog current output increases immunity. (Industrial Terms: Electrical Noise, EMI/RFI)
Depending on the location of the sensor and controller, when using an analog voltage output, one may see a voltage drop in the output signal due to the resistance in the wire increasing from a long cable run. In an analog current output, the current strength in the loop is not affected by voltage drops in the wiring because the current output at the negative terminal of the loop must return to the positive terminal of the supply. (Industrial Terms: Voltage Drop, Current Loop)
Finally, when using a 4-20mA analog current output, you have the ability to detect if you have a broken wire because your signal will now go to 0mA. There are supplementary analog voltage outputs that address this issue, such as 1-5V or 2-10V.
The Basics of 4-20 mA Analog Current Loops
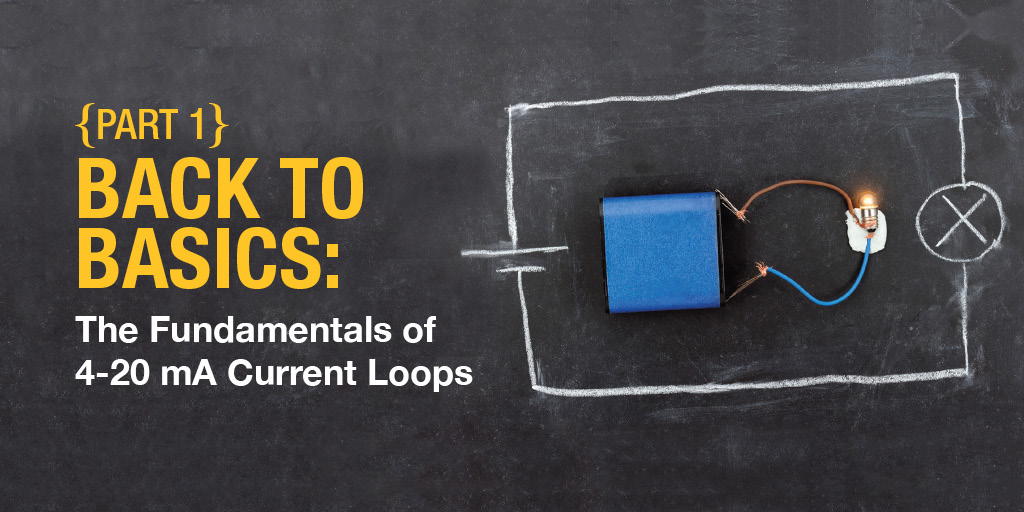
In the world of process control, there are countless types of process inputs. Thermocouples and RTDs provide direct temperature readings while digital signals like Modbus® provide precise control and display of process variables. Analog signals, in which process information is transmitted via varying amounts of voltage or current, are the predominant type of input in industries requiring process control today. Of all the analog signals that can be used to transmit process information, by far, the 4-20 mA current loop is the dominant standard.
Since the 4-20 mA current loop standard has become predominant in the process control industry, many people do not understand the basics of setting up and using it. Not knowing the basics can cost you money when it comes time to make decisions about displaying and controlling the process. Grasping the history, operation, advantages, and disadvantages of the 4-20 mA loop will help you understand why it is the dominant standard in the industry and allow you to make informed decisions about controlling your process.
A Bit of History
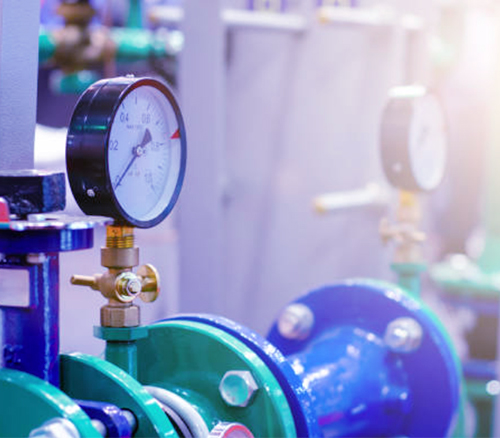
Before the advent of electronic integrated circuits, process control was an entirely mechanical endeavor. Plants used pneumatic control signals in which controllers were powered by varying pressures of compressed air. Eventually, 3-15 psi air compression became the standard for several reasons:
-
It was very expensive to design a system that detected pressure signals below 3 psi.
-
Signals below 3 psi would have been undetectable.
-
It was easier to distinguish a live signal (3 psi) from a problem in the system (0 psi).
In the 1950s, as electronic systems became less expensive, current input became the preferred and more effective process control signal. The 4-20 mA range then became the standard for the same reasons 3-15 psi had.
How Does a 4-20 mA Current Loop Work?
To understand what a 4-20 mA direct current (DC) loop is and how it works, we will need to know a bit of math. Don't worry; we will not dive into any advanced electrical engineering formulas. In fact, the formula we need is relatively simple: V = I x R. This is Ohm's Law. This is saying that voltage (V) is equal to current (I) times resistance (R) (“I” stands for Intensité de Courant, French for Current Intensity). This is the fundamental equation in electrical engineering.
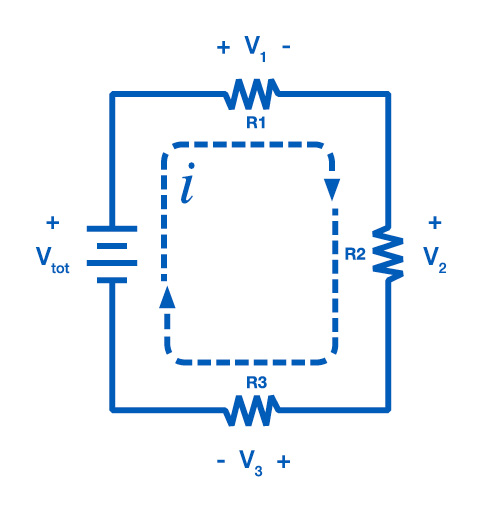
Figure 1. Simple DC Circuit
Consider the simple DC circuit above, consisting of a power supply and three loads. A current loop requires a voltage to drive the current. This is provided by the supply, with the voltage of the source labeled as Vtot. The current then travels through the loop, passing through each load. The voltage drop across each load can be calculated from Ohm's Law. The voltage V1 dropped across R1 is:
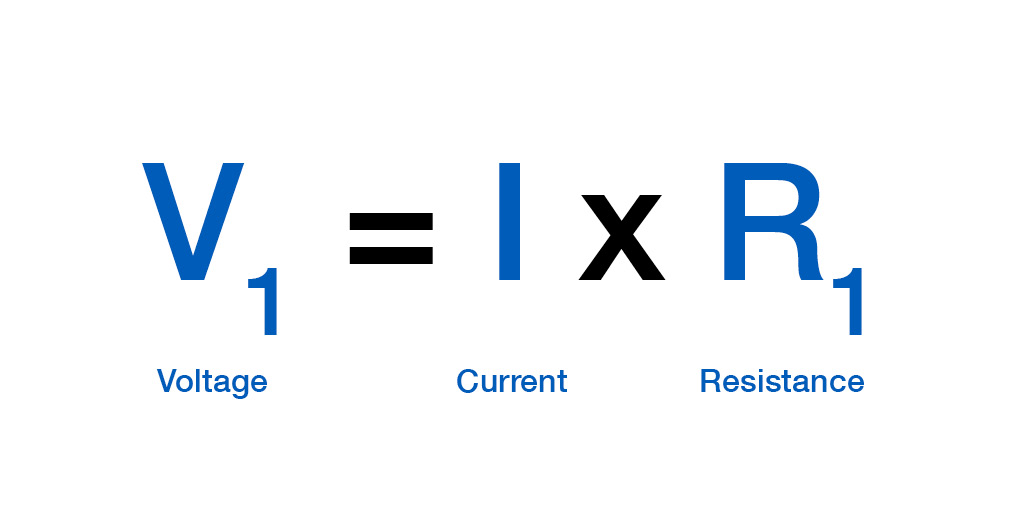
Figure 2. Ohm's Law
Every element in the loop either provides voltage or suffers a voltage drop. However, the current, "I," is the same everywhere in the loop. This is the crucial principle of the 4-20 mA loop. The current is the same at all places throughout the loop. It can be difficult to understand why the current is constant, so consider your home's water system for comparison. There is a certain pressure in the water lines pushing water towards your house.
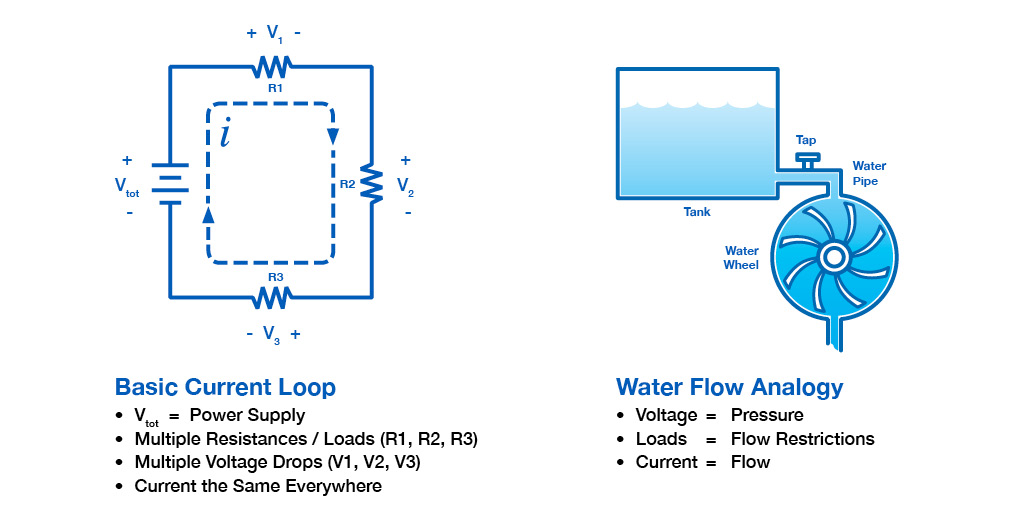
Figure 3. Current / Water Flow Voltage
In an analogous way, it acts like a pressure, pushing current through the circuit. When a faucet inside your house is turned on, there will be a subsequent flow of water. The flow of water is analogous to the flow of electrons, or current. The ability of the pressure to push water through the pipes is limited by bends and restrictions in the lines. These restrictions limit the amount of flow in the pipe, similar to how a resistor limits current. The flow through the pipe, and similarly, the current through the wire, is constant throughout the entire system, even though the pressure, and voltage, will decrease at various points. This is why using current as a means of transmitting process information is so reliable.
Components of a 4-20 mA Current Loop
Now that you understand how and why current is used, you can begin to understand exactly what the loop is for.
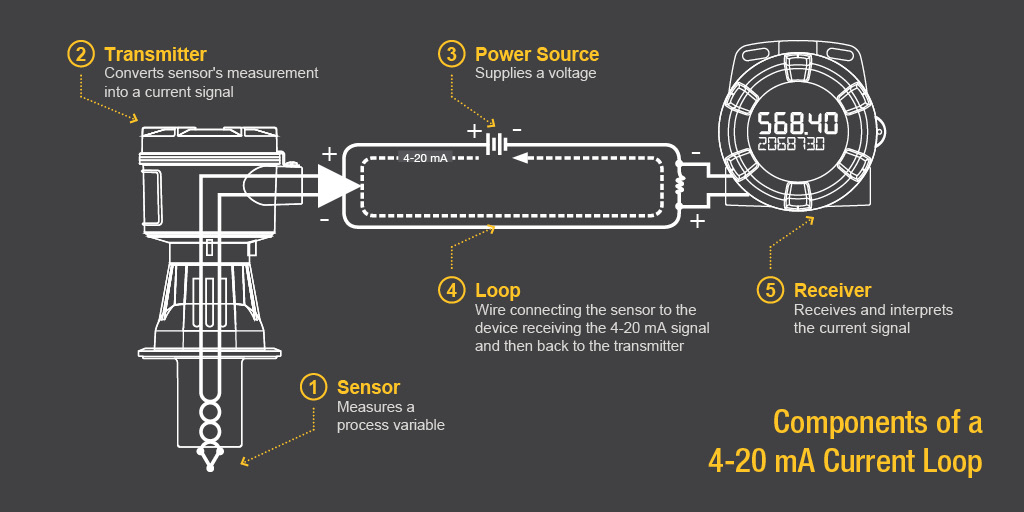
Figure 4. Components of a 4-20 mA Current Loop
1.Sensor
First, there needs to be some kind of sensor that measures a process variable. A sensor commonly measures temperature, humidity, flow, level, or pressure. The technology used for the sensor will vary significantly depending on what exactly is being measured.
2.Transmitter
Second, whatever the sensor is monitoring, there needs to be a way to convert its measurement into a current signal, ranging from 4 to 20 milliamps. This is where the transmitter comes into play. For example, if a sensor is measuring the height of a tank that is 10m long, the transmitter will convert 0 m when the tank is empty to 4mA and transmit. Conversely, the transmitter will convert 10m when the tank is full to 20mA and then transmit a 20 milliamp signal. If the tank is half full, the transmitter will output a signal at the halfway point, or 12 milliamps. (Instrumentation Term: 4-20mA Transmitter)
3.Power Source
In order for the signal to be generated, there needs to be a power source, just as in the analogous water system, there needs to be a source of water pressure. Keep in mind that the power source needs to be outputting direct current (meaning the current only runs in one direction). There are a variety of common voltages used with 4-20 mA current loops (9, 12, 24, etc.) depending on the particular setup. When deciding what voltage of power supply to use for your particular setup, be sure to consider that the power supply voltage must be at least 10% greater than the sum of the voltage drops of the accompanying components (transmitter, receiver, and even the wire). Using an inadequate power supply can lead to equipment damage. (Instrumentation Term: Loop Power Supply)
4.Loop
In addition to an adequate VDC supply, there also needs to be a loop, which involves the actual wire connecting the sensor to the device receiving the 4-20 mA signal and then back to the transmitter. The current signal on the loop is regulated by the transmitter according to the sensor's measurement. This component is often overlooked in a current loop setup because wire is the very nature of any modern electronic system, but it needs to be considered when exploring the basics. While the wire itself is a source of resistance causing a voltage drop across the system, this is usually not a concern, as the voltage drop of a piece of wire is very small. However, over long distances (greater than 1000 feet or 300m), it can add up to a significant amount, depending on the thickness (gauge) of the wire. (Instrumentation Term: Loop Wiring)
5.Receiver
Finally, somewhere in the loop there will be a device that can receive and display the current signal. This current signal needs to be converted into units that an operator can readily understand, such as the height (m, ft, etc.) of the liquid in the storage tank or the temperature in °C. This device also needs to either display the information received (for monitoring purposes) or automatically perform a function with that information. Digital displays, controllers, actuators, and valves are common devices to incorporate into the loop. (Instrumentation Term: Loop Indicator, Process Controller)
These components are all that is needed to complete a 4-20 mA current loop. The sensor measures a process variable, the transmitter converts that measurement to a current signal, the signal travels through a wire loop to the receiver, and the receiver displays or performs a task with the signal received.
Advantages and Disadvantages of 4-20 mA Loops
Part of the challenge of working in an industry that requires process control is determining whether the advantages outweigh the disadvantages. Making the right decision can save both time and money.
Advantages
-
4-20 mA current loops are a popular standard across many industries.
-
It is the simplest option to connect and configure.
-
Uses fewer wires and connections than other signals, which significantly reduces upfront costs.
-
Better at traveling long distances, as current does not degrade over long connections like voltage does.
-
Less susceptible to surrounding electrical noise.
-
Since 4 mA is equal to 0% output, it is extremely simple to detect faults in the system.
Disadvantages
-
Current loops can only transmit one specific process signal.
-
Multiple loops must be created in situations where there are numerous variables to be transmitted. Running too many wires can lead to issues with ground loops if the independent loops are not properly isolated.
-
These isolation requirements become exponentially more complex as the number of loops grows. (Instrumentation Term: Ground Loop, Signal Isolation)
4-20 mA Current Loop Overview
The 4-20 mA current loop is a prevalent process control signal across many industries. It is an ideal method of transmitting process information because the current does not change as it travels from transmitter to receiver. The current loop is also much simpler and cost-effective. However, voltage drops and the number of process variables needing to be monitored can affect the cost and complexity of the loop. Knowing these basics, you will be able to make more informed decisions about controlling the process in your plant.
DLK Trading Service Company Limited
Address: G6/14 Tran Van Giau, Le Minh Xuan Ward, Binh Chanh District, Ho Chi Minh City
Office: 111/7 Vuon Lai, Phu Tho Hoa Ward, Tan Phu District, Ho Chi Minh City
Website: https://dlk.com.vn/
Email: info@dlk.com.vn
Hotline: 070 357 0101 – 093 279 2697