A differential pressure sensor measures the pressure difference between two points, helping to monitor and adjust systems like HVAC, dust filtration, and fluid control. In industry, it is used to optimize processes and protect equipment.
1. General Introduction
1.1. Definition of Differential Pressure Sensor
A differential pressure sensor is a measuring device designed to detect the pressure difference between two points in a system. The measurement results are often used to calculate flow rate, liquid levels, or to monitor the performance of devices such as pumps, valves, or filters.
1.2. Basic Operating Principle
The differential pressure sensor works by comparing the pressures at two input points (high and low pressure). The difference in pressure affects a sensing element (such as a diaphragm, pressure gauge, or electronic sensor), which generates an output signal. This signal can be in the form of voltage, current, or digital data to be sent to control and monitoring systems.
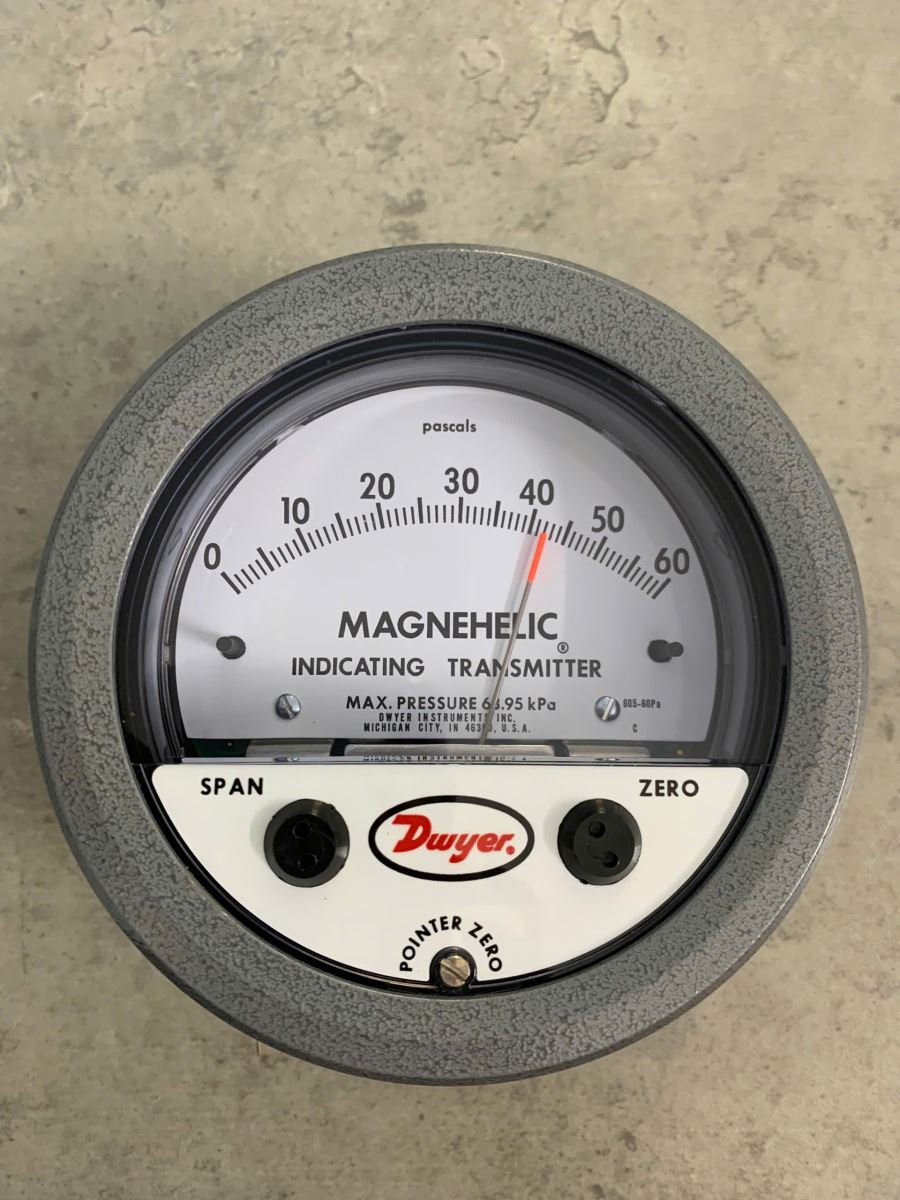
1.3. Common Types of Differential Pressure Sensors
Mechanical Differential Pressure Sensors: Work based on the mechanical movement of a diaphragm.
Electronic Differential Pressure Sensors: Use piezoelectric or capacitive technology to detect pressure.
Differential Pressure Sensors for Small Pressure Differences: Specialized for applications requiring very small pressure differences, commonly used in clean rooms or the pharmaceutical industry.
Smart Differential Pressure Sensors: Integrate IoT connectivity, self-diagnosis, and automatic calibration.
1.4. Role in Industry
Differential pressure sensors are essential components in many industrial applications. They ensure safety, optimize performance, and provide continuous monitoring for operating systems. From monitoring fluid levels in tanks, measuring flow in pipes, to checking filter performance, differential pressure sensors offer outstanding accuracy and quick response.
2. Structure and Operating Principle
2.1. Structure of a Differential Pressure Sensor
A differential pressure sensor typically consists of the following main components:
-
Diaphragm: The central part, made from elastic or metallic materials, that separates and measures the pressure difference between two areas.
-
Pressure Chambers: Two separate chambers connected to the two points where pressure is being measured (high pressure and low pressure).
-
Transducer: Converts the mechanical deformation of the diaphragm into an electrical or analog signal.
-
Signal Processing Circuit: Amplifies and processes the output signal for transmission to the control system or display.
-
Protective Housing: Made from corrosion-resistant materials like stainless steel or aluminum alloy, protecting the internal components from environmental factors.
2.2. Operating Principle
The differential pressure sensor works by comparing the pressure between two points:
-
Pressure Difference Measurement: The pressures at the two measurement points are transmitted to the pressure chambers via connecting ports.
-
Diaphragm Deformation: The pressure difference creates force that deforms the diaphragm. The degree of deformation is proportional to the pressure difference.
-
Signal Conversion: The deformation of the diaphragm is measured and converted by the transducer into an electrical signal, usually a current (4-20 mA) or digital signal (Modbus, HART).
-
Signal Output: The output signal is sent to the controller or monitoring system for analysis and display.
2.3. Methods of Differential Pressure Measurement
-
Mechanical Method: Based on the mechanical movement of the diaphragm or piston.
-
Capacitive Method: Measures the change in capacitance as the diaphragm moves.
-
Piezoelectric Sensor Method: Converts mechanical pressure into an electrical signal using the piezoelectric effect.
2.4. Advantages of Design and Operating Principle
-
High Accuracy: Works well under various pressure conditions.
-
Flexible Design: Easy to install and integrate into systems.
-
High Durability: Performs well in harsh environments (high temperatures, corrosive environments).
-
Fast and Continuous Signal Output.
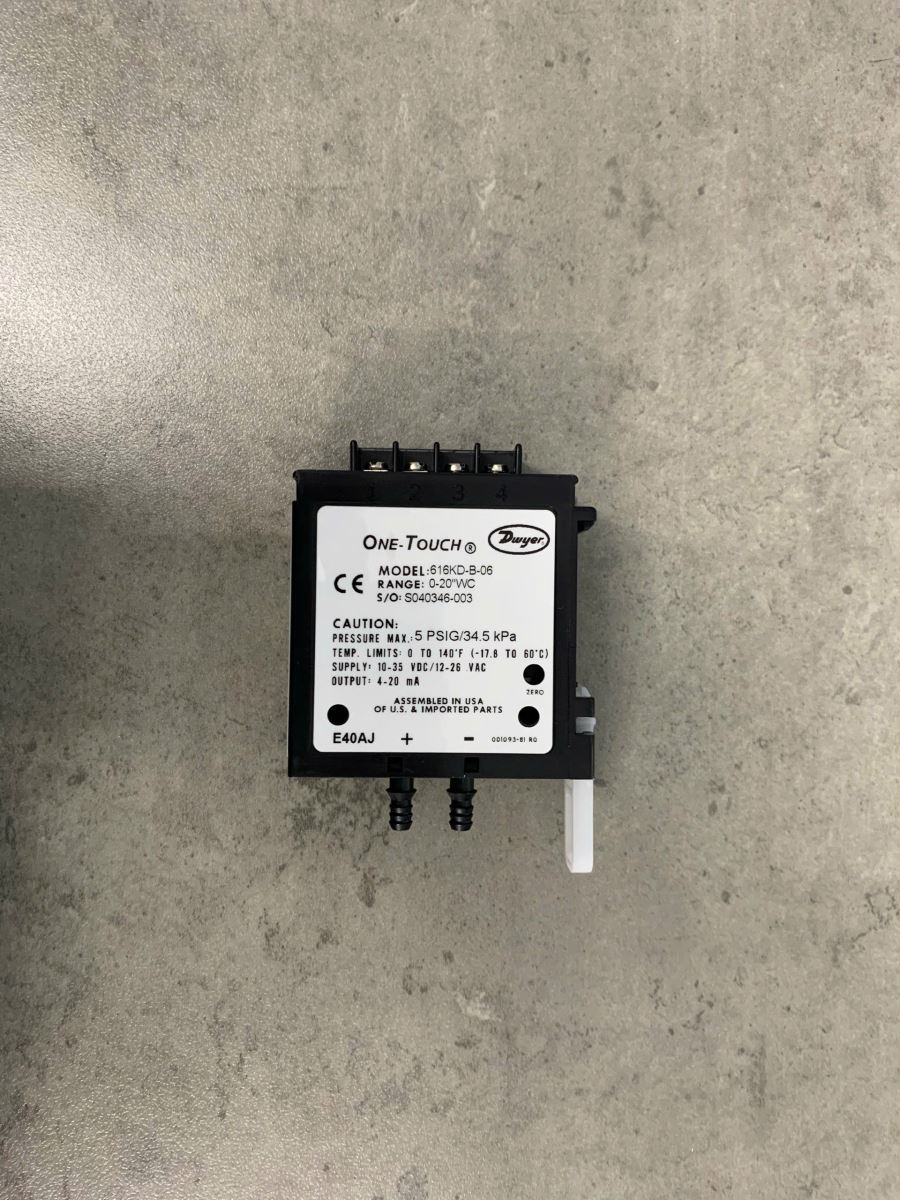
3. Industrial Applications
Differential pressure sensors are widely used in many industries due to their ability to accurately and reliably measure pressure differences. Below are some of the key applications:
3.1. In HVAC (Heating, Ventilation, and Air Conditioning Systems)
-
Monitoring pressure differences in ventilation and air conditioning systems to ensure effective air circulation.
-
Measuring filter performance: Detecting when filters need to be cleaned or replaced.
-
Automatic control of air flow through pipes and valves.
3.2. In Oil, Gas, and Chemical Industries
-
Monitoring pressure differences in pipelines to ensure stable and safe flow.
-
Measuring pressure differences across filters in oil and chemical filtration processes.
-
Pressure control in tanks to prevent dangerous overpressure situations.
3.3. In Water and Wastewater Treatment
-
Measuring water levels in tanks or towers using pressure differences.
-
Monitoring pump or filtration system performance.
-
Detecting leaks or blockages in water pipelines.
3.4. In Food and Beverage Industry
-
Monitoring pressure in storage tanks to ensure safety and quality standards.
-
Checking filter performance during production and packaging.
-
Regulating pressure in CO2 or steam pipelines during production.
3.5. In Energy Technology
-
Measuring pressure in boilers and turbine systems to optimize energy efficiency.
-
Monitoring pressure in solar or wind energy systems to ensure stable operation.
-
Detecting failures in energy systems by monitoring pressure differences.
3.6. In Pharmaceuticals and Healthcare
-
Controlling pressure in clean rooms to ensure pharmaceutical manufacturing standards.
-
Monitoring pressure in clean gas systems in surgical rooms or healthcare areas.
3.7. In Other Special Applications
-
Monitoring pressure in scientific research and experimental systems.
-
Monitoring pressure in transportation systems, such as trains, airplanes, or electric vehicles.
-
Differential pressure sensors help optimize performance and ensure safety, reducing maintenance costs across various sectors.
4. Benefits and Limitations of Differential Pressure Sensors
4.1. Benefits
Differential pressure sensors provide practical advantages for industrial applications due to the following reasons:
-
High Accuracy: Measures pressure differences precisely, even in complex systems.
-
Versatile Applications: Suitable for many industries, including oil, gas, energy, water treatment, healthcare, and food production.
-
Economic Efficiency: Helps reduce operating and maintenance costs by detecting issues early.
-
Stable Operation in Harsh Environments: Modern sensors can withstand high temperatures, high pressure, and corrosive environments.
-
Standard Output Signals: Supports common signal transmission protocols like 4-20 mA, HART, Modbus, making them compatible with most modern control systems.
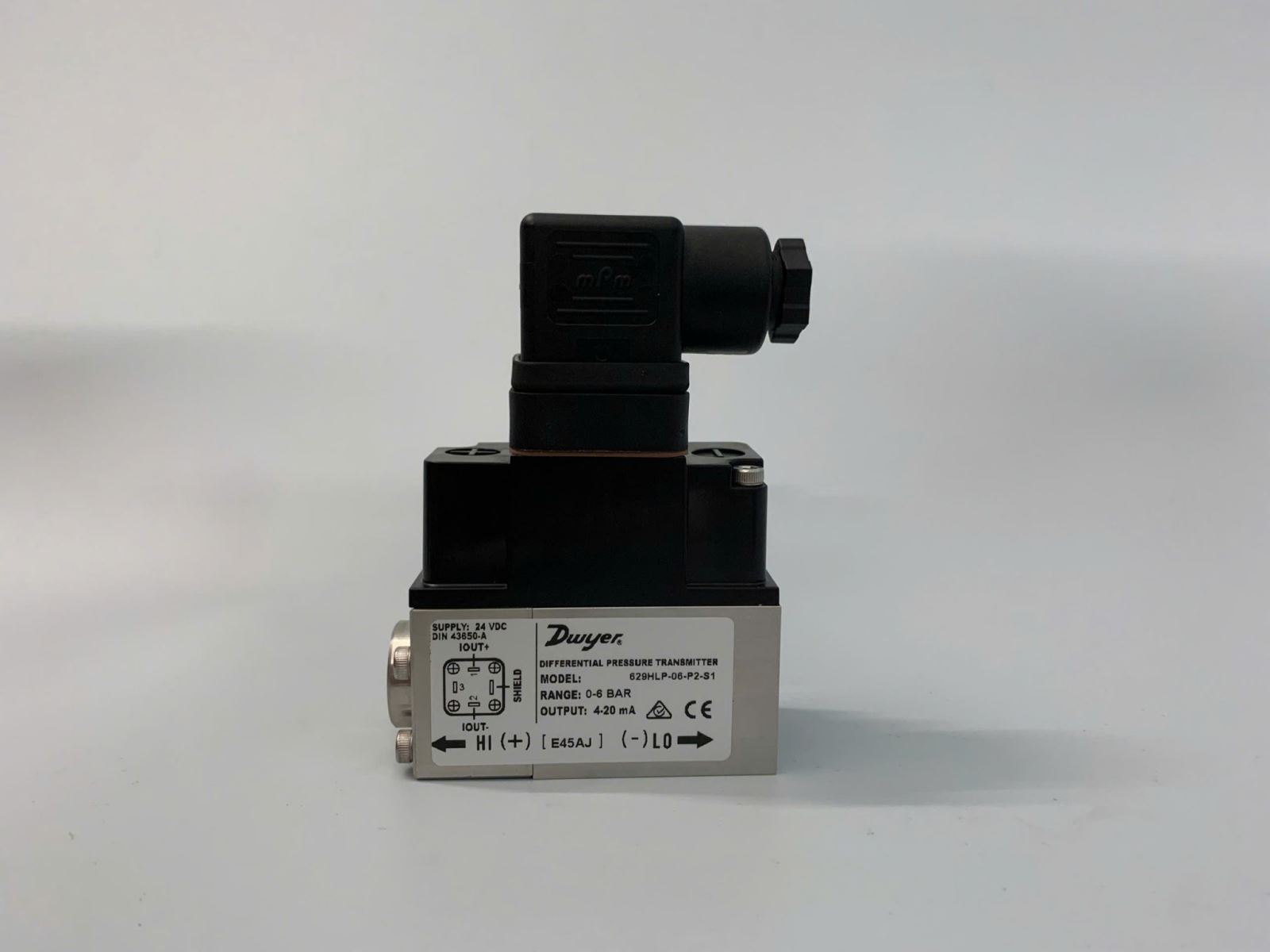
4.2. Limitations
Despite their many benefits, differential pressure sensors also have some limitations:
-
Environmental Sensitivity: Sensors may be affected by temperature changes, vibrations, or aggressive chemicals if not properly designed.
-
Calibration Requirements: Regular calibration is needed to maintain accuracy, adding maintenance costs.
-
Measurement Limits: Some sensors may not be able to measure very small or very large pressure differences, so the correct sensor must be chosen.
-
High Initial Investment: High-quality sensors, especially those with IoT features, may have higher upfront costs compared to regular measuring devices.
-
Technical Expertise Required: Installation, operation, and maintenance require skilled technicians, particularly for complex systems.
4.3. Overview
Differential pressure sensors are indispensable in many industries due to their ability to provide accurate and flexible measurements. However, to achieve the best results, it’s important to select the right sensor and ensure the environment is suitable for its operation.
5. Criteria for Selecting Differential Pressure Sensors
When choosing a differential pressure sensor, it’s important to consider technical and environmental factors. Here are key criteria:
5.1. Measurement Range
Select a sensor with a measurement range that meets the minimum and maximum pressure differences in the system. Avoid sensors with too wide a range, as this can reduce accuracy.
Example: HVAC systems often have small pressure differences, so a low-range sensor (0-500 Pa) is needed.
In the oil and gas industry, larger ranges (0-100 bar) may be required.
5.2. Accuracy and Sensitivity
Ensure high accuracy for applications like clean room monitoring or quality control systems. Check the error margin, usually specified in product documentation (e.g., ±0.1%).
5.3. Material and Environmental Resistance
Choose sensor materials based on the operating environment:
-
Corrosive environments: Use sensors with stainless steel diaphragms and corrosion-resistant housings.
-
High-temperature environments: Select sensors designed to withstand high temperatures (up to 400°C if necessary).
-
Vibration-sensitive environments: Use sensors with vibration-resistant designs.
5.4. Output Signal and Communication
Ensure the sensor’s output signal is compatible with the control system:
-
Analog output: 4-20 mA, 0-10 V.
-
Digital output: HART, Modbus, Profibus. Check if the sensor supports integration with automation or IoT systems.
5.5. Response Speed
For systems that require real-time monitoring (e.g., turbines, compressors), the sensor should have a fast response time.
5.6. Size and Installation Compatibility
Ensure the sensor’s size fits the available space. Check the connection method (thread, flange, or pipe fitting) for compatibility with the system.
5.7. Brand and Certification
Choose sensors from reputable manufacturers like Dwyer, Honeywell, Omega, or Siemens. Ensure the sensor meets international standards (ISO, CE, ATEX for explosive environments).
5.8. Maintenance and Longevity
Opt for sensors with low maintenance requirements and high durability to reduce replacement costs.
5.9. Price and Budget
Consider the cost based on the features and durability of the product. Weigh the initial investment against long-term operational savings.
When selecting a differential pressure sensor, clearly define the system’s needs, working environment, and technical requirements. The right sensor will optimize system performance and reduce operational costs.
6. Technology Trends and the Future of Differential Pressure Sensors
Technological advancements and growing industrial needs continue to enhance the development of differential pressure sensors. Below are trends and future directions:
6.1. IoT Integration and Smart Technology
-
Wireless Connectivity: Modern differential pressure sensors integrate IoT technologies, enabling wireless data transmission via Wi-Fi, Zigbee, or Bluetooth.
-
Real-time Data Analysis: Pressure data is sent directly to control systems or the cloud for analysis and forecasting.
-
Predictive Maintenance: Helps prevent downtime by predicting failures.
-
Automatic Calibration: Some smart sensors can calibrate automatically without manual intervention.
6.2. Miniaturization
Sensors are becoming more compact, ideal for applications with limited space, such as medical devices or electronics.
6.3. Increased Durability for Harsh Environments
Sensors are designed to withstand extreme temperatures (from -40°C to 800°C), chemical exposure, and vibrations, making them suitable for the oil, gas, and chemical industries.
6.4. Industry 4.0 Applications
Integration with SCADA and ERP systems: Sensors are integrated into production management systems for optimal workflow and energy savings.
Full Automation: Differential pressure sensors play a vital role in intelligent manufacturing lines, ensuring automated monitoring and control.
6.5. Wireless Differential Pressure Sensors
Wireless sensors minimize the need for wiring, making them easy to install in hard-to-reach areas, particularly in mobile applications like vehicles or robots.
6.6. Data Security
With IoT integration, data security becomes crucial. Advanced encryption and security protocols will be essential to protect sensitive data.
6.7. Eco-friendly Sensors
There is a growing trend to develop sensors using recyclable materials, with designs focused on low power consumption to support sustainability.
7. Conclusion and Introduction to DLK Trading Service Company Limited
7.1. Conclusion
Differential pressure sensors play an essential role in modern industries by optimizing production processes, ensuring safety, and improving operational efficiency. From understanding how they work and their applications in various fields, to selecting the right sensor based on specific needs, it is clear that these devices provide valuable support for industries.
7.2. DLK Trading Service Company Limited – Your Trusted Partner
DLK Trading and Services Co., Ltd. proudly offers high-quality differential pressure sensors from renowned global brands like Apollo, Dwyer, and Honeywell.
-
Diverse Products: DLK offers a wide range of sensors suitable for various industries, including light industries like HVAC and water treatment, as well as heavy industries such as oil, gas, energy, and chemicals.
-
Optimization Solutions: DLK’s team of experts is always ready to help customers select the most suitable products for their needs and operating conditions.
-
Commitment to Quality: DLK products meet international standards (ISO, CE, ATEX), ensuring durability, accuracy, and stable operation in harsh environments.
-
After-Sales Service: In addition to providing equipment, DLK offers support services, including installation and maintenance.
>>> View detailed Differential Pressure Sensor products: HERE
Advice from DLK:
Don't hesitate to contact DLK for advice on selecting the most suitable differential pressure sensor solution for your company's specific needs.
Investing in quality equipment from the start will help you:
-
Save on operating costs
-
Increase production efficiency
-
Minimize long-term risks
Contact DLK Trading Service Company Limited
Address: G6/14 Tran Van Giau, Le Minh Xuan Commune, Binh Chanh District, Ho Chi Minh City
Head Office: 111/7 Vuon Lai, Phu Tho Hoa Ward, Tan Phu District, Ho Chi Minh City
Website: https://dlk.com.vn/l
Email: info@dlk.com.vn
Hotline: 070 357 0101 – 093 279 2697
Let DLK accompany you on your journey to building and developing modern, sustainable industrial systems!